Более чем 100-летний опыт технического прогресса позволил нам стать ведущим производителем в области частотных преобразователей, сервоприводов, систем управления и робототехники.
Ipeka Automation Oy
Challenge
Ipeka utilizes drive and control components from Yaskawa
The Finnish baking equipment manufacturer has developed a machine for the fully automated packaging of tin loaves. At the heart of this complex design are drive and control components from Yaskawa.
Ipeka’s new development, the “Loafmaster 50”, enables fully automated bagging of up to 50 tin loaves per minute – no mean feat: A movable arm pushes the bread into the previously opened bag, which is then sealed with a clip. The machine is very flexible and can be used both for whole and sliced loaves. The packaging material can take the form of different plastics, foils or paper. The smooth and precise execution of all processing steps is ensured by powerful control and drive components from Yaskawa.
Exacting customer requirements
Ipeka opted for Yaskawa solutions for five main reasons: the high availability of drives and controls, the ability to program according to the international EN/IEC standard as well as the speed and flexibility of the control system with regard to additional axes. Ipeka also attributed great importance to machine safety: Following an emergency stop, the safety function of the servo drives ensures that the machine can be restarted from the exact point reached before the stop.
The final factor influencing the Finnish company’s decision was the presence of a local expert in the form of the Finnish branch of the Lönne Group in Helsinki, who could assist in the selection of suitable Yaskawa components. As an established partner to Yaskawa, the Norway-based Lönne Group provides an expert presence across the Scandinavian region.
Solution
Machine controllers of the MP series
The various sequences are managed by an MP2300siec machine controller. As part of Yaskawa MP series, this all-in-one machine controller combines all the functions necessary for the machine process in a single platform: motion control and PLC functions, inputs and outputs as well as sequential logic and process algorithms. This controller integration reduces system costs, improves performance, minimizes the space required in the control cabinet and standardizes programming. The MotionWorks IEC2 software and the Yaskawa Toolbox facilitate the programming of the machine controller. The software was designed to be especially easy to use and is based on the global EN/IEC 61131-3 standard for PLC programming.
Sigma-5 servo system series
Accurate movements are ensured by three Sigma-5 servo drives with outputs of 0.4 kW, 1.3 kW and 4 kW. These servo drives combine with the controller to form a cohesive control and drive system. The rapid data communication between the machine controller and the servo drives is conducted via a MECHATROLINK-II real-time Ethernet interface. Within this overall system, the Sigma-5 drive controllers automatically adapt to different load scenarios: The servomotor runs at a constant speed or the speed set, regardless of the current load.
Sigma-5 is a servo drive consisting of servo motors, servo amplifiers and the powerful Sigma-Win+ engineering tool. The series includes rotary motors, direct drives and linear motors. The standard types combine high positioning accuracy with short positioning times. The rotary servo motors are available with drive outputs of 3 W to 55 kW. Sigma-5 motors can cover a wide variety of applications of any size in many industries. Optional encoder cards are also available for many models in the series.
Result
AC drives of the V1000 series
Four V1000 AC drives with Ethernet/IP cards complete the Yaskawa package for the “Loafmaster 50”. Where permanent magnet motors offer precise and secure control, YASKAWA’s V1000 inverter drive represents a solution that is as reliable as it is efficient. With its highly dynamic current vector control (open loop vector), it drives both induction motors and permanent magnet synchronous motors in an output range of 100 W to 15 kW.
As a compact inverter drive, the V1000 is characterized by its minimal space requirements. These compact dimensions are supplemented by the ability to install multiple devices side-by-side, meaning that the inverters require even less space in the control cabinet.
Conclusion
A powerful package of Yaskawa drive and control components ensures the precise execution of all processing steps performed by Ipeka’s new “Loafmaster 50” packaging machine. The main factors influencing the decision of the Ipeka experts were availability, programmability according to EN/IEC standards as well as the speed and flexibility of the control system.
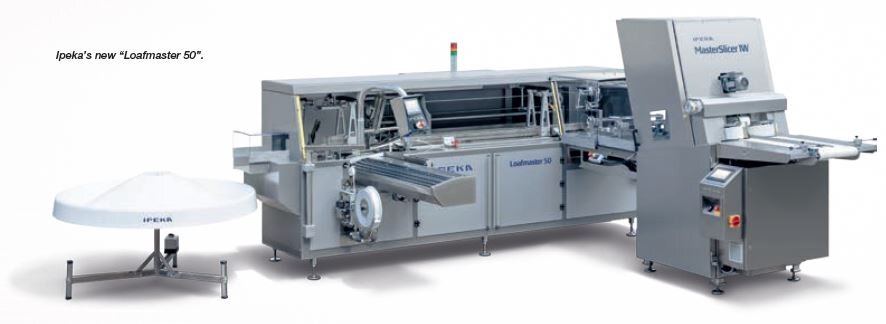