Более чем 100-летний опыт технического прогресса позволил нам стать ведущим производителем в области частотных преобразователей, сервоприводов, систем управления и робототехники.
Your production. Your choice. Our best.
Sigma-7 Servo Drives
Choose improved efficiency for your application
The intelligent system design of our Sigma-7 series ensures high overall efficiency and performance of your machinery and equipment. Sigma-7 servo drives are easy to implement, commission and use. Sophisticated functions like vibration suppression reduce stress on machine parts and significantly improve throughput.
Seven reasons for Sigma-7
Wide power range
- Very compact motors from 50 W to 15 kW
- Linear motors iron core and ironless with a peak force up to 7,560 N
- Direct drives with torques from 2 Nm up to 600 Nm
Lower production costs
- Speed loop bandwidth of 3.1 kHz
- Shorter settling time, reduced positioning time, higher throughput
Higher performance
- Overload 350 % for 3 – 5 seconds
- High peak torque, fast acceleration
Energy savings and higher productivity
- High peak torque, fast acceleration, no amplifier oversizing
- Lightweight mechanics
Smooth integration of mandatory legal safety standards
- The STO function is implemented by default in all Sigma-7 series servo amplifiers
- Build safer machines - Sigma-7 safety modules satisfy the requirements of SIL3/PLe (Cat. 3)
- The functions SS1, SS2, SOS and SLS are standard in each safety module
- 3 different option modules are available with up to 14 safety functions
Very low heat generation
- Optimized magnetic circuit improves motor efficiency
- Improved motor efficiency reduces heat generation by about 20 %
- Ambient temperature from -5 to 55 °C (max. 60 °C with derating)
Next level 24-bit absolute encoder for maximum accuracy
- Resolution of 16 million pulses per revolution for extremely precise positioning
Very high precision teamed up with fast, smooth operation
- Ripple compensation for highest demands in smoothness and dynamics
- Even for machines for which speed loop gains cannot be set high
Even more reliability for your production
- More than 22 million servo systems in the field
- Improved machine reliability, reduced service and maintenance costs, less downtime
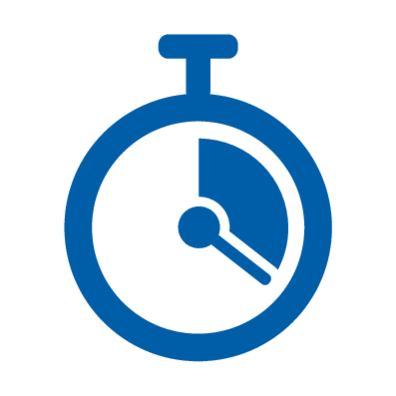
Quick setup in just 3 minutes
Presets in the amplifier software simplify commissioning. A ‚tuning-less‘ function allows immediate use without the need for complex parametrisation or special knowledge of control equipment, while an auto-tuning function ensures quick adjustment.
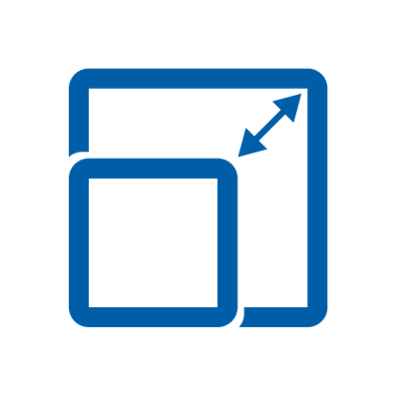
Space saving
New book-style housing supports gapfree, side-by-side installation of amplifiers even in small spaces. This makes it possible to realize high performance density inside a cabinet. The needed space is reduced to a minimum, allowing it and the drive electronics to be integrated in the machine.
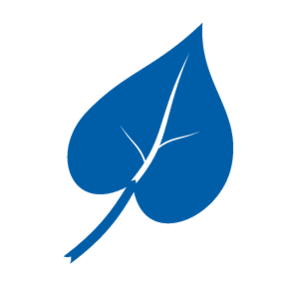
Eco friendly
Motor efficiency reduces heat generation by up to 20 %. The possible DC power coupling of axes allows energy sharing and energy savings of up to 30 %.
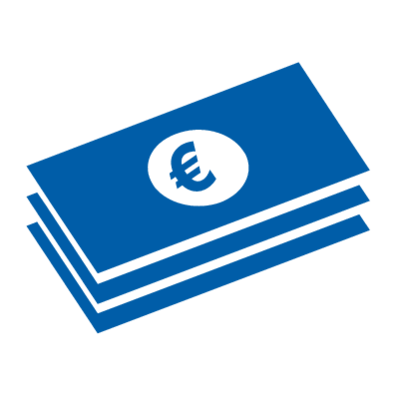
Cost saving
Sigma-7 reduces the overall costs by providing faster machine setup, higher throughput with more products in less time and reduced machine downtimes due to it's high reliability.
Savings through performance
With a best in class frequency response of 3.1 kHz, Sigma-7 SERVOPACKs can reduce settling time to less than 4 ms. Compared to a standard system with 40 ms settling time as an example, a pick & place unit based on Sigma-7 components can save a significant amount of money.
~23 €
Additional revenue per hour
~375 €
Additional revenue per 16 hours
>1,875 €
Additional revenue per 5 days
>93k €
Additional revenue per year
40 ms settling time using standard servo drives
Axis length | Move | Settle | Move | Settle | Time per part | Parts per minute | Parts per hour | Price per part | Revenue per hour |
---|---|---|---|---|---|---|---|---|---|
X = 200 mm | 0.5 s | 0.04 s | 0.5 s | 0.04 s | 1.56 s | 38.46 | 2307 | 0.1 € | 230.77 € |
X = 200 mm | 0.2 s | 0.04 s | 0.2 s | 0.04 s | |||||
Total | 0.7 s | 0.08 s | 0.7 s | 0.08 s |
4 ms settling time using Sigma-7
Axis length | Move | Settle | Move | Settle | Time per part | Parts per minute | Parts per hour | Price per part | Revenue per hour |
---|---|---|---|---|---|---|---|---|---|
X = 200 mm | 0.5 s | 0.004 s | 0.5 s | 0.004 s | 1.416 s | 42.37 | 2542 | 0.1 € | 254.24 € |
X = 200 mm | 0.2 s | 0.004 s | 0.2 s | 0.004 s | |||||
Total | 0.7 s | 0.008 s | 0.7 s | 0.008 s |
Next generation servo systems
With more than 22 million servo systems in the field, we have a lot of experience and technical know-how in motion and control. The Result: Excellent performance and an extremely low fault rate.
With our Sigma-7 series, we managed to create a masterpiece in reliable precision performance. Thanks to its smart features, start-up is possible in just a few minutes.
Quick, application specific drive adjustments and maximised product output are guaranteed.
SERVOPACKs
- Single & dual axis amplifier
- One amplifier for linear & rotary motors
- SIL 3 for STO, PL-e CAT 3
- Speed frequency response: 3.1 kHz
- Advanced safety functions SS1, SS2, SLS
- Feedback options
- Ripple compensation, vibration suppression, etc.
Servomotors
- 24-bit high-resolution encoder installed
- High efficiency, low heat generation
- Three motor models available
- Low inertia SMG7A up to 7 kW
- Medium inertia SGM7J up to 1.5 kW
- Medium inertia SGM7G up to 15 kW
Bundles and individual components
We can offer our customers bundles as well as individual components for many applications in the automation industry.
High performance machine controller for automation technology. Our machine controllers manage complex systems with servo and AC drives. Highspeed communication provides high-performance and high-accuracy motion control, even for complex movements.
- Up to 62 axes
- Communication: Modbus TCP/IP, MECHATROLINK-III, Ethernet (100 Mbit/s)
- PLCopen function blocks
- Reusable code library
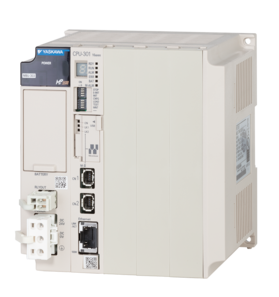
The 4-axis high-speed robot MOTOMAN MPP3 with parallel kinematic system combines the speed of the delta design with a high payload capacity and a large working range.
The MOTOMAN MPK is a high-speed, 5-axis picking robot that provides superior performance and reliability for food handling, picking, packing and other high-speed material handling applications.
- Minimal footprint
- Fast acceleration and high speed increase productivity
- Optional vision and conveyor tracking for maximum flexibility
- Manage every system component with one software package, running on one motion controller.
- Migrate a motion axis from servos to robots and back again, without changing the application code.
- Do it all with the same IEC 61131-3 programming format that your team is already skilled and comfortable with utilizing.
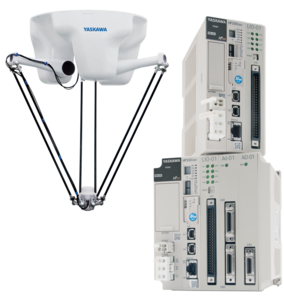
VIPA professional touch panels with display sizes from 4.3“ to 12.1“, operating system Windows Embedded CE 6.0 and Runtime Movicon 11 can be used universally.
VIPA eco panels in 4 different display sizes from 4.3“ to 15“ are designed for maximum reliability and flexibility, as well as longevity and quality.
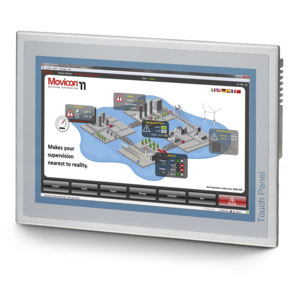
Safety in Motion
Yaskawa offers a new generation of safety modules, which are geared to your requirements. They follow with SIL3/PLe and FSoE (FailSafe over EtherCAT) the latest standards of the industry.
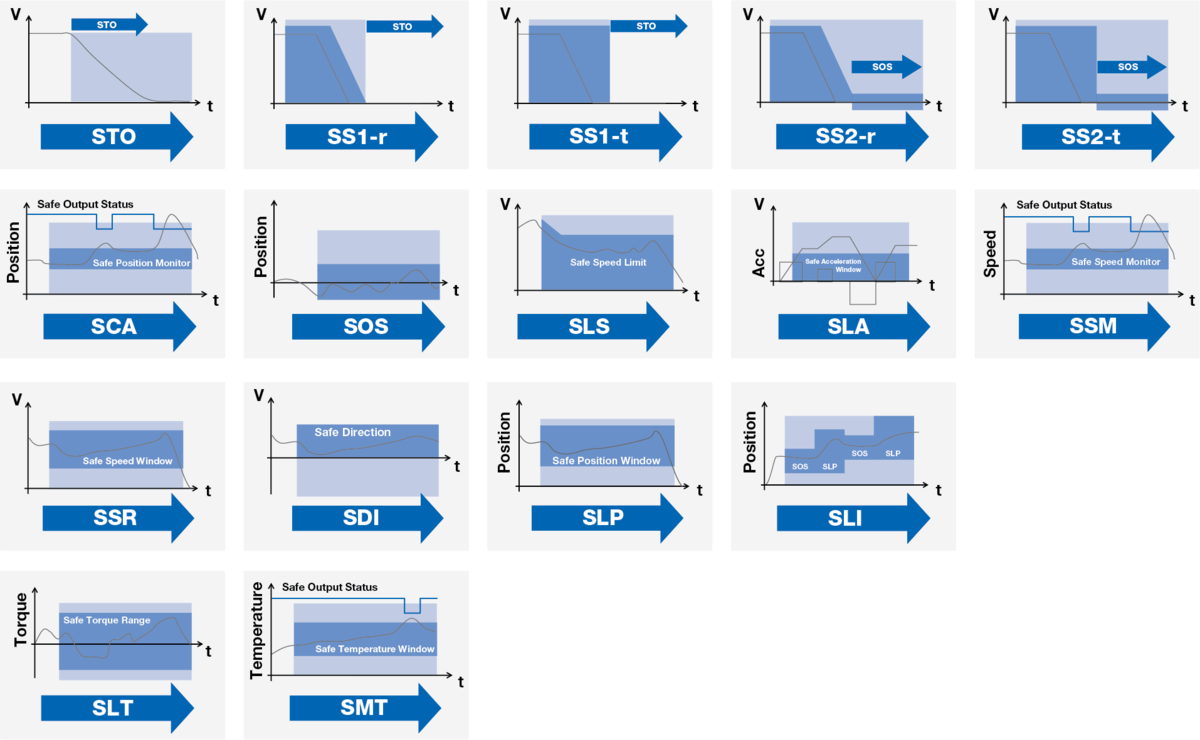
Advanced Safety Module
When it comes to safety, compromises are not an option. That‘s why Yaskawa Sigma-7 servo drives easily integrate into FSoE safety concepts. From the 14 available safety functions, 10 of them can work in parallel. This allows secure and easy control even for the most complex solutions. Sigma-7 safety cards enable high performance safe motion for your application.
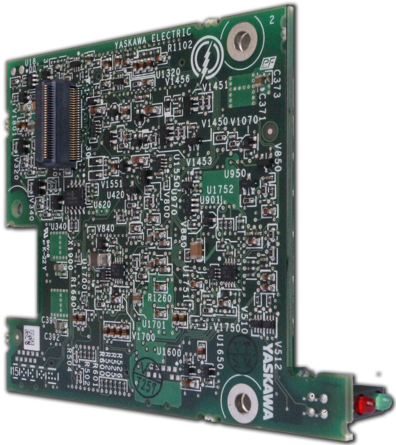
- 14 freely configurable safety functions up to SIL3/PLe
- Up to 10 safety functions can be active in parallel
- Full safety function access over FSoE
- Quick and easy parametrization with certified Yaskawa configuration tool
- Internal parameter and plausibility check ensuring high integrity safety solutions
Advanced Safety Module with attached I/O terminal block
The safety module with attached I/O terminal block provides even more planning freedom and flexibility. The terminal block adds 6 safe digital I/O and 2 safe analog input channels to the card. Additionally, it enables the functions Safe Motor Temperature and Safely Limited Torque and offers a total of 16 safety functions.
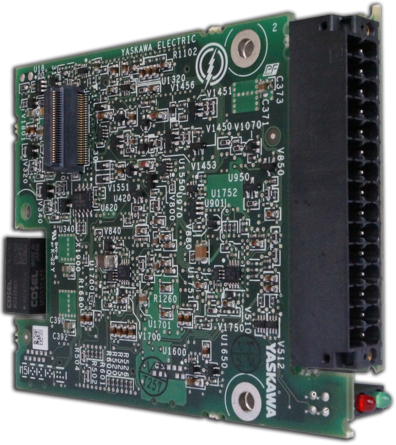
- 16 safety functions: STO, SS1-r, SS1-t, SS2-r, SS2-t, SOS, SLS, SSM, SDI, SLP, SSR, SLI, SCA, SLA, SLT, SMT
- Up to 10 safety functions can be active in parallel
- Full safety function access over FSoE
- Quick and easy parametrization with certified Yaskawa configuration tool
- Internal parameter and plausibility check ensuring high integrity safety solutions
- 6 safe digital I/O cannels and 2 SIL2/PLd capable analog I/Os onboard
- PT1000 input for Safe Motor Temperature function
- Analog torque sensor input for Safely Limited Torque
- Activation of safety features without Safety PLC
Already know what you need?
If you already know what you need and just want to make sure we offer the perfect Sigma-7 package, go ahead to the configurator. You will also find the technical data and any downloads you might need - be it CAD files for designing your machine, manuals, CAE files, brochures or software.
Curious? Questions?
Fill out and send the form. Then we will contact you as soon as possible and provide you with the information you want and need. Looking forward to your inquiry.