Более чем 100-летний опыт технического прогресса позволил нам стать ведущим производителем в области частотных преобразователей, сервоприводов, систем управления и робототехники.
From blank profile to finished component in seconds
At PERI, 18 robots produce scaffolding components fully automatically
It's hard to tell just how much high-tech is in a really good scaffolding. The same goes for the production of the individual components: At PERI, one of the market and quality leaders in the industry, a total of 18 Yaskawa robots weld and assemble ledgers fully automatically.
- Отрасли промышленности
- Construction
- Metalworking
- применения
- Arc Welding
- Material Handling
- Клиент
- Peri
For more than 50 years,
PERI has stood for state-of-the-art technology, innovative strength and customer proximity in the construction industry: With a pioneering technical spirit, the family-owned company supports construction companies, scaffolding contractors and architects with innovative and trend-setting formwork and scaffolding solutions for the new construction, conversion or renovation of buildings and structures. Tailor-made logistics, service and engineering services complete the portfolio.
The PERI UP scaffolding construction kit combines the advantages of frame and modular scaffolding in one integral construction kit. The no less than 500 system components are compatible with each other and can be combined in a flexible manner. With just one scaffolding system, facade, industrial and engineering scaffolders can cover almost all modern scaffolding applications.
High level of automation
The production process also reflects the company's high standards. Modern processes and a high level of automation throughout the company lay the foundations for the highest levels of quality and efficiency right from the start. Recently, the company built the new "scaffolding master plant" in Günzburg, Bavaria-Swabia, and bundled the complete production for PERI UP scaffolding technology at this location.
Since 2016, more than one hundred Motoman robots from Yaskawa have been in use at the plant. "At the PERI plant in Weissenhorn, we have been using many of our Yaskawa robots successfully and consistently for more than 30 years. And yet, before setting up the new production facility, we took a critical look at our robotic setup once again," explains Stephan Schraml, Head of the Technology Centre at the PERI plant in Günzburg. "And it was confirmed: Our robotics requirements are best met by the quality of Yaskawa".
Fully automatic ledger welding system
A further 18 new Yaskawa robots have recently been added to a fully automated handling and welding system. Their task is the fully automatic production of ledgers, which are used hundreds of thousands of times in scaffold construction. Movable wedges ensure convenient and safe assembly. At the same time, they place high demands on the production technology. Stephan Schraml describes them as follows: "Even if you can't see it: Due to the integrated wedges, the design of the components allows only very small tolerances. They must therefore be manufactured with extreme precision.”
Previously, production was partially automated using half a dozen robotic welding systems with a rotary table and manual feed. "This also worked," recalls Schraml, "but with significantly longer cycle times, more logistical effort and less flexibility with regard to the size of the components.
The new ledger welding system now handles the entire manufacturing process, from the individual blanks to the finished component. This includes 100% monitoring of welding parameters, optical seam inspection using cameras, and length and angle measurement. Final palletising for onward transport is fully automated, as is the entire system operation. Only one operator per shift is required to monitor the processes.
By using multiple welding stations in parallel, the system can produce more than a thousand ledgers per shift. The plant was designed to Peri's specifications with optimum use of space. The very complex, space-optimised design is only possible by implementing a wide variety of robot arrangements, such as the use of gantry systems.
On the software side, the FSU safety controller developed and used by Yaskawa-Motoman ensures that the overlapping and often parallel robot sequences run safely and without collision.
The control technology is located on a gallery above the component feed.
Complex processes
The base profiles are fed into the system fully automatically via stanchions, where they are separated, marked and measured in the next work step. In a further station, the components, bolt head and wedge, are fed in by handling robots. After the wedge and bolt head have been joined, the bolt head is welded using the MAG process and the weld quality is then checked inline.
In addition to the coarse forging tolerances of the bolt heads and wedges, the main challenge is the handling of the different profile lengths, which range from 250 to 3,000 mm. The different component lengths are handled by automatic gripper changing systems.
All relevant process and system data is displayed on a custom-designed Yaskawa digital platform in the form of a dashboard on a central monitor. This provides easy system operation and overview.
Robots and plant engineering from Yaskawa
A total of 18 robots work "hand in hand" in the new PERI plant: six high-precision Motoman MH5LS welding robots, each with a payload of 5 kg, and a further twelve MH robots with a daily payload of up to 180 kg. The latter perform a wide range of feeding and handling tasks. Two of them carry the camera systems for automatic component inspection.
The entire system was designed and built by Yaskawa. It is representative of the welding systems of all sizes that Yaskawa has been building in Allershausen near Munich for around four decades. The Allershausen site has just been expanded to include an additional 10,000 square metre hall for systems engineering.
Expectations met
Thanks to their combined system expertise, Yaskawa's robot experts were able to solve all the tasks involved in commissioning the new horizontal ledger welding system in Günzburg. "The system is simply very complex and sophisticated, but it is also very good," is how Stephan Schraml from PERI sums it up. "In the meantime, it has been in operation almost without a hitch and the robots have been very reliable.
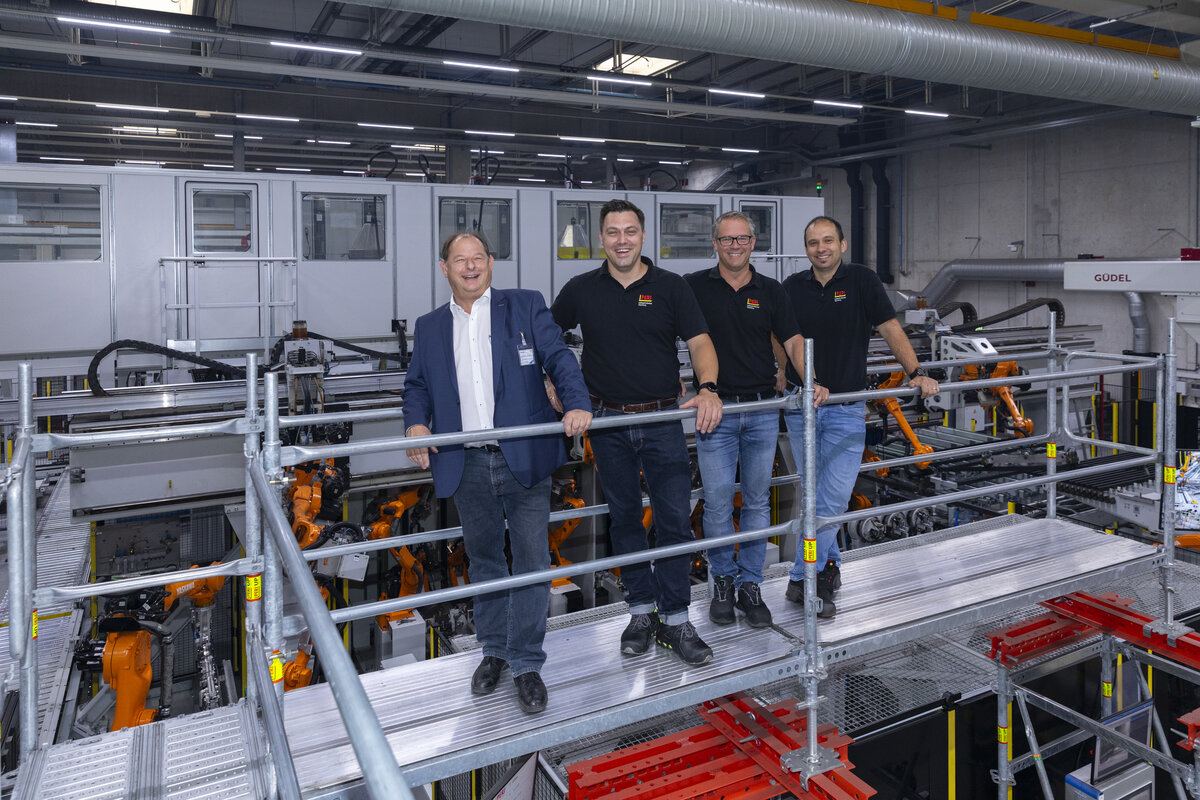
PERI and Yaskawa have been working together successfully for over 30 years (from left to right: Roland Hermann, Christian Merkle (Production Manager), Stephan Schraml (Head of Technology Centre), Wolfgang Urban (Project Manager). (Source: Yaskawa)
Contact:
Roland Hermann
Area Sales Manager GI-Systems, Yaskawa Europe GmbH - Robotics Division, DE-Allershausen
Tel. +49-8166-90-0
Fax +49-8166-90-103
robotics@yaskawa.eu
www.yaskawa.de