Более чем 100-летний опыт технического прогресса позволил нам стать ведущим производителем в области частотных преобразователей, сервоприводов, систем управления и робототехники.
MOTOMAN Robot Controllers
DX200
Reliable Controller for MOTOMAN Robot Systems
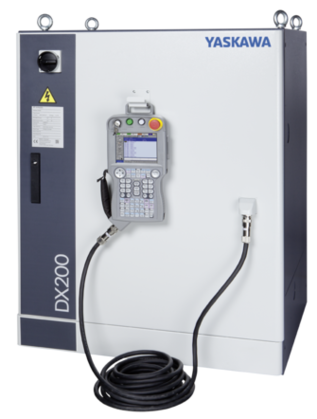
Обзор
The MOTOMAN DX200 is a compact and powerful multi axis and multi tasking controller platform for robots and peripheral motion, like positioners, tracks and gantries, coordinating motion of up to 4 robots (Master/Slave) and additional external axes up to a total of 48 motion axes.
The DX200 controller is used in combination with MPX/MPO Series Painting Robots.
Operation
The DX200 comes with a Touch Screen Teach Pendant (for MPX3500 robots, a special Ex-Proof ATEX teach pendant is available). The operation concept of MOTOMAN robots has been evolved and optimized over the years, based on the experience and feedback of more than 500.000 robots installed in the field so far, resulting in a today's highly efficient operating and programming environment with simple and easy-to-learn flat hierarchy menu structures, hotkeys, quick takeover of teach positions and understandable program structures with simple line based statements. Using the powerful, high level language Inform, specialists can user powerful commands, make excessive use of control logioc or even create sophisticated motion or communication functions or drivers on their own.
Motion Control Technology
A very fast multitasking CPU, an advanced operating system and the Yaskawa Sigma5 high speed servo technology allow high accelerations, fast axis speeds and superior path performance.
The multitasking, non-Windows-based operating system with very fast interpolation cycle does not require virus protection (saving the associated high update/maintenance efforts). The boot time is <40 sec. Thanks to very fast interpolation cycles, all MOTOMAN robots provide excellent path performance. The Advanced Robot Motion (ARM) function dynamically calculates and controls the torque and load of the robot axes, optimises acceleration and speed, eliminates vibrations, adjusts target positions very quickly and enables highly sensitive collision detection. Different interpolation methods, path switching functions and position level control allow precise definition and execution of the robot path. An integrated, very fast soft PLC that is closely interacting with the robot program I/Os can be used to control peripherals or smaller production cells and can potentially make a PLC cell controller obsolete in simple installations.
Controller Hardware
In case of repair, all components can be quickly exchanged (MTTR < 5 min). The compact, industry-proof, stackable controller cabinet (IP54) has an indirect cooling system and is ideally suited for rough industrial environments. Each robot cabinet (Master or Slave) offers comfortable installation space for integration of external axi controllers and servo packs, interfaces and connectors, fieldbus and safety systems, PLC cell control systems or 3rd party application controllers.
Functions and Function Packages (Hardware/Software)
The DX200 offers a variety of function packages (standard, extended, advanced) and application specific Function packages (General, Handling, Painting), single functions (e.g. Servofloat, Machine Vision, Analog Control) and syntax extensions, all of them making programming and commissioning of MOTOMAN robots and their peripheral comfortable and easy.
Machine Safety (MSU/FSU)
The DX200 has a two channel safety system architecture (MSU, Emergency Stop and Safety Signals for safe I/O communication. Safety devices like Safety Scanners or light barrier can be wired directly to the controller. All Teach Pendants provide the obligatory 3 position enabling switches. All robot servo motors are using high precision absolute encoders and spring operated brakes which are closed in the event of an emergency stop - there is no need for cyclical brake tests.
Functional Safety (FSU)
The optional Functional Safety Unit (FSU) is a dual channel safety board and a software, providing options to allow safe moniting of position and speed inside/outside of defined workspace zones (axis ranges, cartesian zones, virtual curtains or protection zones around a tool). The FSU supports definition of a large number of these zones, allowing to model even complex cells layouts or interactions. The FSU considers the complete mechanical structure of the robot including elbows, not only the TCP (Tool Center Point), and allows to model the robot tooling and workpiece, including all these elements into the safe monitoring. The FSU is a powerful tool to reduce installation space and create safe interference zones.
Energy Efficiency and CO2-Footprint
Energy Saving Options, e.g. „Individual Servo-Off“, are available. As an option, DX200 controllers for larger MOTOMAN robot models can be equipped with a condensator-based recuperation unit, leading to a significant energy recovery rate specifically in applications of short motion sequences and many decelerations like spot welding.
Open Communication
The DX200 can be easily integrated into existing networks. The robot controller comes with a set of standard communication interfaces, e.g. two Ethernet ports or digital inputs/outputs, as well as the FTP-capable TCP/IP web server function, allowing to read/set the controller status or enabling remote monitoring or maintenance over the Web. Other digital and analog I/O communication boards are available. The YRC1000 supports interfaces and communication protocols for the Digital Factory / Industry 4.0, e.g. OPC/UA (supporting the VDMA Robotics Companion Specification).
As a worldwide robot manufacturer, Yaskawa supports a unique variety of fieldbus systems, such as Profinet, Interbus, Devicenet, ASI-Bus, Profibus, EthernetIP, ModbusTCP, CCLink, CanOpen, EtherCAT including their safety bus variants, as well as market-specific interfaces such as Euromap. Direct or fieldbus-based communication interfaces are available for a big variety of peripheral devices and equipment, often combined with a HMI integration on the teach pendant, e.g. supporting different weld controllers, grippers, 2D/3D Vision Systems or Force/Torque Sensors.
Open Programming
MOTOMAN Robots with DX200 controllers are open for many programming methods, each of them making sense in their individual applications, markets or environments, such as:
- Teach Pendant (Touchscreen), highly functional and menu/command-line based (Inform III)
- Motologix Function Blocks, embedding robot programming completely in commonly used IEC 61131-based PLC programming environments
- Software Pendant (PC based)
- Offline-Simulationstool MotoSimVRC (OLP) (Device, Cell & Line Level)
- 3rd party Offline-Simulationstools (OLP) (Cell / Line / Plant Simulation Level) and Digital Twin Solutions
- Application related Apps and wizards (e.g. Welding Wizard, PalletSolver, Motologix)
- 3rd party CAD/CAM-Tools (deriving robot code from CAD Data over G-Code post processors)
- Robot Operating System ROS
- 3rd party, cross brand robot programming environments
- API-Interfacing to Scientific PC Programming environments, e.g. Matlab oder LabView
- 2D/2D Machine Vision control, Bin Picking, feature or AI/Neural network based
- Customer developed apps, wizards, visualisations, HMIs, coded by using our Software Development Kits (e.g. Motoplus C/C++, MotoCom32 SDKs)
- Application specific function packages including more than 120 functions
- High productivity
- Low integration costs
- High reliability and energy efficiency
Загрузки
Имя | |||
Flyer Controller DX200
Robot Controller MOTOMAN DX200 Data sheet | английский |
Data sheet | английский | |
Flyer Steuerung DX200
Robotersteuerung MOTOMAN DX200 Data sheet | немецкий |
Data sheet | немецкий | |
Flyer FunctionalSafetyUnit FSU
Improved Safety Functions with integrated Safety Controller Data sheet | английский |
Data sheet | английский | |
Flyer FunktionaleSicherheitssteuerung FSU
Verbesserte Sicherheitsfunktionen mit integrierter Sicherheitssteuerung Data sheet | немецкий |
Data sheet | немецкий | |
PL-Zertifikat TUEV DX200 MachineSafetyBoard
Zertifikat TUEV DX200 - Machine Safety Board Certification | английский |
Certification | английский | |
PL-Zertfikat TUEV DX200 FSU FunctionalSafetyBoard
Zerfikat TUEV Robotersteuerung DX200 Funktionale FSU Functional Safety Board Certification | английский |
Certification | английский | |
Brochure DX200 Functions & Packages Brochures | английский | Brochures | английский | |
DX200_2D.zip CAD/CAE | | CAD/CAE | ||
DX200_3D.zip CAD/CAE | | CAD/CAE |